Optymalizacja utrzymania taboru kolejowego poprzez zastosowanie druku 3D
Firmy z branży kolejowej zaczęły wdrażać technologie druku 3D do wykonywania prac produkcyjnych i konserwacyjnych. Zbudowanie dobrego pociągu, który wytrzyma dystans i zapewni pasażerom komfort, wymaga dużej ilości komponentów bardzo wysokiej jakości. Sektor kolejowy coraz częściej zwraca się w stronę wytwarzania przyrostowego, bardziej znanego jako drukowanie 3D. Firmy kolejowe i analitycy twierdzą, że technologia - która była tworzona przez ostatnie trzy dekady - może pomóc w odświeżeniu rynku przestarzałych części zamiennych i skrócić czas ich produkcji nawet o 95%. Jak skuteczna jest ta technologia i na ile wspiera branżę?
Produkcja taboru kolejowego jest kolejnym obszarem zastosowania druku 3D, który sprawdza się w wytwarzaniu coraz większej liczby elementów dotychczas wytwarzanych z metalu. Korzyści z druku 3D w branży kolejowej stają się coraz bardziej widoczne. Firmy z branży chętnie wdrażają technologię, aby rozwiązywać problemy z przestarzałymi częściami zamiennymi oraz długimi czasami dostaw narzędzi i komponentów do użytkownika końcowego. Nie bez znaczenia obok uniezależnienia się od dostawców niszowych części jest również skrócenie czasu przy prototypowaniu nowych rozwiązań. W ciągu ostatnich 12 miesięcy wiele firm kolejowych, w tym Deutsche Bahn, Bombardier i Angel Trains, zainwestowało w druk 3D.
Zalety druku 3D w produkcji części zamiennych w taborze kolejowym
Druk 3D pozwala na wytwarzanie części maszyn, linii produkcyjnych czy też różnego typu uchwytów niezbędnych w utrzymaniu ruchu. Znaczny wzrost filamentów wykorzystywanych do druku 3D w ostatnim okresie, zwiększył zakres zastosowań. Teraz druk daje możliwość szybkiej rekonstrukcji części maszyn, które ulegają zniszczeniu w wyniku eksploatacji, a są kosztowne, trudno je sprowadzić czy też są niedostępne na rynku. Przemysłowe drukarki 3D pozwalają na drukowanie z wytrzymałych tworzyw, spełniających rygory bezpieczeństwa, między innymi takich jak certyfikaty niepalności. Części wykonane z inżynieryjnych materiałów są lżejsze niż te z aluminium, a przy tym nie ustępują pod względem wytrzymałości. Dzięki drukarce 3D mamy możliwość wykonania części na żądanie (zlecenie usługi wydruku) lub bezpośrednio w zakładzie produkcyjnym bez konieczności uruchamiania długotrwałych procesów zakupowych. Druk 3D daje możliwość wykonania elementów w niskich seriach lub pojedynczych sztuk za ułamek kosztów produkcji tradycyjnymi metodami, np. obróbką CNC.
Zalety druku 3D:
- ulepszanie dotychczasowych rozwiązań bez generowania dodatkowych kosztów
- minimalizacja ryzyka w obszarze łańcucha dostaw
- optymalizacja procesu napraw i eliminowania przestarzałych części
- zmniejszenie kosztów produkcji narzędzi, osprzętu i części zamiennych
- sprawne reagowanie na nowe potrzeby klientów
Innowacyjne rozwiązania w niemieckich kolejach dzięki technologii druku 3D
Na szeroką skalę druk 3D znajduje zastosowanie w kolejach niemieckich, które dzięki nowoczesnej strukturze zarządzania wydajniej sterują procesami wprowadzania innowacyjnych rozwiązań w kolejnictwie.
Głowica drukująca przesuwa się od lewej do prawej. Dysza precyzyjnie nakłada materiał. To, co początkowo wygląda jak prosty dwuwymiarowy prostokąt, powoli nabiera kształtu. Po kilku godzinach pracy drukarka 3D wykonała nowy zagłówek do siedziska w ICE dla Deutsche Bahn. To tylko jedna ze 100 różnych części, które DB już produkuje w procesie druku 3D. Szczególny nacisk położono m.in. na: koła wentylatorów, zagłówki do pociągów regionalnych, szeroką gamę obudów, a nawet małe części nieoczywiste dla kolei, takie jak: część zamienne do ekspresów do kawy i wieszaki na ubrania w przedziałach pociągu.
W kolejnictwie niemieckim proces drukowania 3D pozwala na szybkie drukowanie części zamiennych, które w innym przypadku wiązałyby się z długimi terminami dostaw lub w ogóle nie byłyby dostępne. Oznacza to, że pociągi mogą szybciej wracać na tory, a przestoje są krótsze. Wszystkie komponenty z drukarki 3D przed użyciem przechodzą rozbudowane testy, np. test wytrzymałości zmęczeniowej. Podczas gdy, pierwsze drukowane części były wykonane wyłącznie z tworzywa sztucznego, głównie z poliamidu. Obecnie różnego rodzaje elementy drukowane są z innych materiałów np. z nylonu z włóknem węglowym lub niepalnym ABS.
Według raportu EY (Ernst & Young Global Limited) 16% firm z branży logistycznej i transportowej wykorzystuje drukowanie 3D do produkcji części zamiennych. Co kieruje tym założeniem? Dlaczego branże kolejowe inwestuję w przemysłowy druku 3D?
W większości przypadków firmy kolejowe mają do czynienia z sytuacją, w której zaprzestano produkcji wymaganych części zamiennych lub producenci nie prowadzą już działalności. Druk 3D to jedyna technologia, która może rozwiązać takie problemy. Dodatkowo nie wymaga ona dodatkowych narzędzi, takich jak formy do tworzenia części.
Druk 3D części zamiennych znacznie skraca czas produkcji przestarzałych elementów, w niektórych przypadkach nawet o 95%. Proces ten jest również często kojarzony z inżynierią odwrotną, zwłaszcza w przypadku utraty pierwotnego projektu części lub niemożności pozyskania dostawcy.
Prototyp siedziska kolejowego wydrukowanego przez Omni3D na drukarce Factory 2.0
Firma Polgár Kft. potrzebowała prototypu, aby zweryfikować nowy projekt siedziska do pociągu. W procesie projektowania zawsze pojawiają się punkty krytyczne, które należy zweryfikować w skali 1:1. Prototyp siedziska został wykonany przez firmę Omni3D na maszynie Factory 2.0 Urządzenie, jako jedno z niewielu, spełnia dwa kryteria niezbędne do realizacji tego wydruku – duże pole robocze (500 x 500 x 500 mm ) oraz możliwość druku z podporami (2 głowice). Wygenerowanie podpór było niezbędne do prawidłowego odwzorowania geometrii siedziska.
“Wytworzenie funkcjonalnego prototypu pozwala na precyzyjne przetestowanie modelu. Wcześniej było to dla nas praktycznie niemożliwe ze względu na bardzo długi czas oczekiwania na wytworzenie części metodą tradycyjną. Teraz, dzięki zastosowaniu druku 3D, możemy zmienić projekt zaraz po wydrukowaniu pierwszych elementów. Przy projekcie fotela okazało się, na przykład, że niektóre ruchome części (np. wysuwany kosz na śmieci) – nie działały poprawnie. Zostało to pominięte w projekcie CAD.”
Polgár Kft.
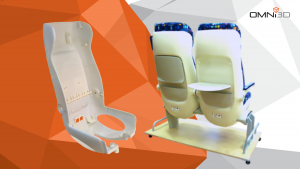
Wzrasta liczba firm z branży kolejowej inwestujących w technologie przyrostowe. Producenci i serwisy taborów kolejowych dostrzegają korzyści wdrożenia druku 3D oraz szacują oszczędności, jakie niesie produkcja z użyciem drukarki 3D.
Zastosowanie druku 3D w przemyśle kolejowym:
Jeżeli Państwa firma szuka możliwości oszczędności czasu i redukcji kosztów zapraszam do kontaktu. Przeprowadzimy bezpłatny audyt i przedstawimy dopasowaną do Państwa potrzeb ofertę przemysłowych drukarek 3D Omni3D.
Autor: Jacek Krzyżanowski
Kontakt:
LinkedIn: Jacek Krzyżanowski
m. +48 886 618 690
e-mail: jk@omni3d.com