How 3D Printing helps in production of special parts?
The Vicim company is an international manufacturer of parts for the automotive industry. The customer asked Omni3D to print a prototype of the designed part by using flexible material. It should be made in a 1: 1 scale.
In this case, one of the most important issuce for the customers’ R&D was to use the FDM / FFF technology. 3D printing in this case gives the possibility of free changes in the design and continuous improvement of the prototype in terms of ergonomics and usability. Compared to the traditional manufacturing method, 3D printing was an option not only becouse of the financially advantageous, but also gives the opportunity to individually refine a design with an unusual shapes and materials.
The design has been prepared for the purpose of visual and aesthetic assessment and to illustrate the homogeneity of the elements used. To ensure the consistency of individual elements and maintain the dedicated „design”. An additional goal was to check the influence of aerodynamics (analysis of potential resistances and forces acting on the fastening elements) and possible deformations caused by air resistance. After accepting the assumed shape, mass production will be launched.
Sebastian Fabisiak Project Engineer, Vicim
Solution
Specialists from Omni3D’s printroom used the TPU-93Shore filament for printing – it is a material that reflects the design assumptions, and its properties provide a certain flexibility. For pritning the mud flap, Omni3D’s team used the Omni500 LITE Production System – which, thanks to double gear system, ensures good and reliable material feeding during printing.
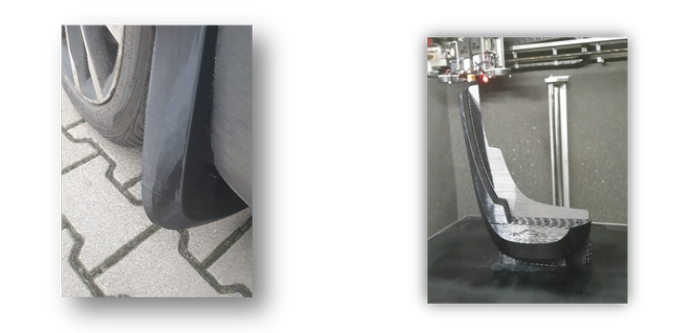
Effect
The printed mud flap met the customer’s requirements and became an element used in everyday production process.
SECTOR | Przemysł lekki |
CLIENT | Vicim |
CATEGORY | Final Parts |
FILAMENT | TPU-93A |
PRINTING TIME | 22 h |
WEIGHT | 213 g |
DIMENSIONS | 330 x 260 cm |
Want to know more about the possibilities of 3D printing?
Contact us!