Omni3D Air Circulation System™
In the world of 3D printing, more and more about the power of industrial printers is a closed, actively heated chamber. This factor gives above-average possibilities of monitoring and maintaining an appropriate temperature environment in the printing process.
Many customers are convinced that a heated chamber and an appropriate air circulation system are the key aspects determining purchasing decisions when choosing a 3D printer. It is hard to disagree with this, because many printer manufacturers on the Polish market offer only passive heating of the chamber – using a work table. Therefore, we have developed our own warm air circulation system. Thanks to the use of a 2 kW heater, we are able to assess how our printout will behave both during printing and while cooling down. The very placement of the heater at the bottom of the device is crucial. Hot air coming out through regular cutouts in the heater housing is distributed upwards thanks to the high-efficiency fan, and it does not accumulate only within the working platform.
This creates a kind of cyclone with a controlled temperature in the working space – even up to 70 degrees C. This solution prevents the problem of deformation of the print during printing, because hot air is not directly blown onto the print. In fact, we are able to print large-size elements from demanding materials that shrink during printing, such as ABS. The Omni3D Air Circulation System is perfect for situations where the printouts are expected to last several dozen or even several hundred hours of continuous printing. It becomes especially important when we want precise and repeatable models with a certain degree of filling. To illustrate the above statement, I will use an infographics prepared by our specialists from the Print-Room department.
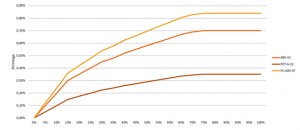
Find out more about Omni3D Unique Points: