Optimization of the production line thanks to the Omni3D printer
3D printing allows you to quickly check the accuracy of the dimensions before ordering an expensive form for the production of the tool. Thanks to the Omni3D printer, the customer could try out the designed tool and apply corrections before ordering the production of the final product.
The goal of one of the manufacturers in the automotive industry was to optimize the production process of one of the lines. The company needed transport of delicate electronic components between the production hall buildings. The tray used for this had to be precisely adjusted to the size of the components, light, and also able to be stacked together with other trays. The company wanted to be sure that the design was correct before ordering a thermoforming tool, which is used to manufacture the final products and decided to check it out with Omni3D.
“The devices we produce consist of many elements that we have to transport between the production halls. The blister must be perfectly matched to the components and our infrastructure to ensure safety during transport. Thanks to Factory 2.0, we can verify the correctness of designs on an ongoing basis and introduce corrections to them, before we submit the blister design for final production. „- Customer’s statement
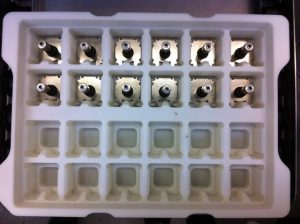
3D printing was a natural choice for the complex geometry of the design. The model was made on a 3D printer – Factory 2.0 in FFF technology, using ABS-42 material. Thanks to the use of 3D printing, the client could evaluate the designed model of the tool and apply corrections before ordering the final thermoforming tool.
3D print specification
INDUSTRY | Automotive |
CATEGORY | Prototyping |
MATERIAL | ABS-42 |
PRINT TIME | 62 h |
SIZE | 360 x 260 x 75 mm |
WEIGHT | 900 g |
Do you want to know more about the use of 3D printing in production?
Contact our specialist or ask for 3D printing on demand