3D printing in the production of the final parts of the racing car
The PRz Racing Team decided to use elements printed on a 3D printer for their project. The task of Omni3D was to print an element that would be adapted to the requirements of racing cars. The inlet manifold is an element exposed to vibrations, high temperatures of approx. 100°C and chemicals.
Task
The Formula Student initiative initiated cooperation between the PRz Racing Team and Omni3D. Young enthusiasts faced the task of designing and then building the intake manifold. The biggest problem was adjusting the collector parameters to the most efficient engine operation. Complicated geometry, tightness of the system and its strength and stiffness (element exposed to vibrations, high temperatures around 100 degrees C and chemicals). A very important factor in guaranteeing success was the attempt to reduce the weight of the component compared to traditionally manufactured parts.
Description of the problem
The task was to print an element that would be adapted to the requirements of racing cars. The selected material had to be characterized by high temperature resistance, but also stiffness. A very important factor was the reduction of the weight of the element compared to traditionally manufactured parts and the ability to freely change the geometry.
Solution
The best solution to this challenge was the use of 3D printing, which, offering low costs and the possibility of several iterations of the project in a short time, gave the opportunity to conduct several tests. The model was printed on a Factory 2.0 NET printer using CF PA-12 filament. Already the first tests confirmed the design correctness of the element and efficiency as intended. The carbon fiber reinforced polyamide used provided the expected strength of the printed element.
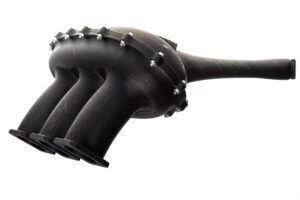
Effect
The 3D printed intake manifold is 1.5 kg lighter than a traditional aluminum component. The data based on the mass point simulation shows that thanks to the 3D printing technology, the weight reduction directly contributed to the better performance of the racing car. What’s more, thanks to the freedom of geometric changes, we have created a fully adapted model to obtain the best possible air flow. 3D printing turned out to be the best choice for the production of final parts for the new PRZ Racing Car-03.
Print specification
INDUSTRY | Automotive |
CLIENT | PRz Racing Team |
CATEGORY | Prototyping, low-volume production, final product |
MATERIAL | CF-PA-12 |
PRINT TIME | 65 h |
WEIGHT | 570 g (0,2 layer) |
SIZE | 291 x 290 x 226 mm + 291 x 290 |
Do you want to know more about the use of 3D printing in production?
Contact our specialist or ask for 3D printing on demand